A critical part of human exisistence, knifemaking dates back thousands of years. Around 3000 BC, during the Bronze age, is when this practice was thought to have truly started. Most blades and tools were made out of copper and bronze at the time. The Iron Age, which began around 1200 BC, brought about the use of iron as the choice for durable material. But the growing reliance on these tools during the medieval period is what shifted forging from barbaric to pure craftsmanship. Blacksmiths from Europe and Asia developed some of the most revered swords and daggers, including the legendary katana and European longsword, during this era.
Then, the Industrial Revolution provided enormous progress in manufacturing and mass production, and blades were not immune. Since consistency in the process freed up time to explore new designs, and steel was more readily available, this timeframe in history witnessed an explosion in intricate craftsmanship. But the approach to mass production drove down prices, and coincidently, the need for repairs to those trusted tools. Why pay for repairs when a new knife cost nearly the same amount?
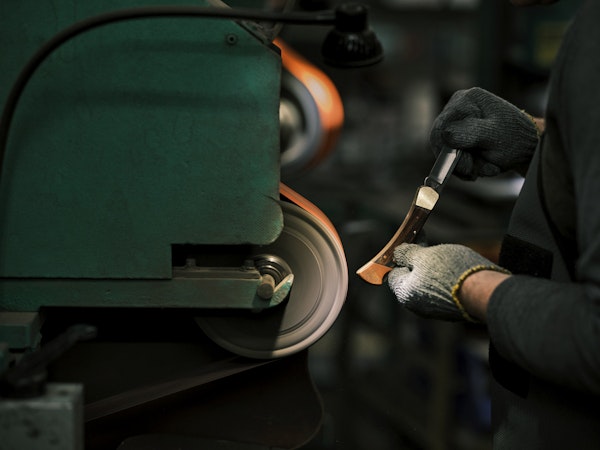
“Bringing that knife back to life, that is what I enjoy,” Sam “Lukky” Carr explains. Carr has worked for Buck Knives for over 12 years. He works alongside Danny Peretti in the warranty department. Carr and Peretti receive some very old knives. None date back to the Iron Age, but quite a few knives land on their work benches from the 1960s and 70s. The Buck Knives Forever Warranty mostly caters to families whose knives are passed down through generations. The department revives pieces of family history. That is why repairs are meaningful.
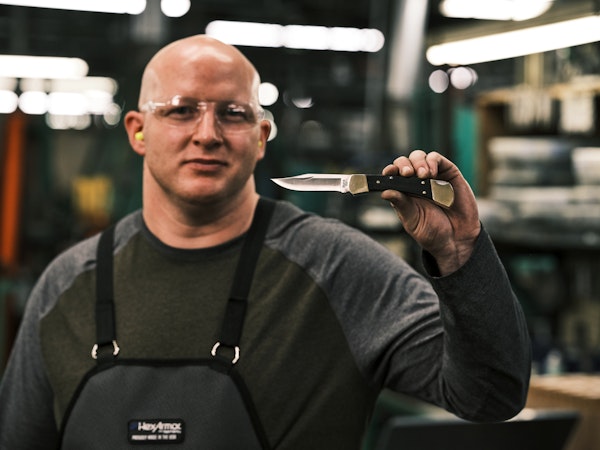
Carr’s day starts at 530 am. He grabs a new box of knives that have been shipped in from all over and cuts into it. Each knife comes equipped with personal instructions from the customers. Some need a new blade. There are a few re-sharpening requests. And the more involved inlay replacements are always a part of the que. Carr tries to get through as much as he can before the Buck Knives Factory Store opens to the public. Once that happens, requests walk in off the street and it gets even busier. Regardless of where they come from, or how involved they may be, he likes the evaluation of it all. The diagnosis of the problem is what keeps Carr focused. “Tearing down a knife is not hard, making it functional is the hard part,” he says.
Compared to Danny Peretti, a 47-year knifemaking veteran and department lead, Carr is still relatively green when it comes to that diagnosis process. Peretti’s teaching style is very relaxed, and he allows Carr to learn on his own, only providing guidance when sought. But 47 years of experience creates instinctive attention to detail, and Carr wants to absorb as much as he can from Peretti. “I feel like the karate kid, and he is Mr. Myagi,” Carr jokes.
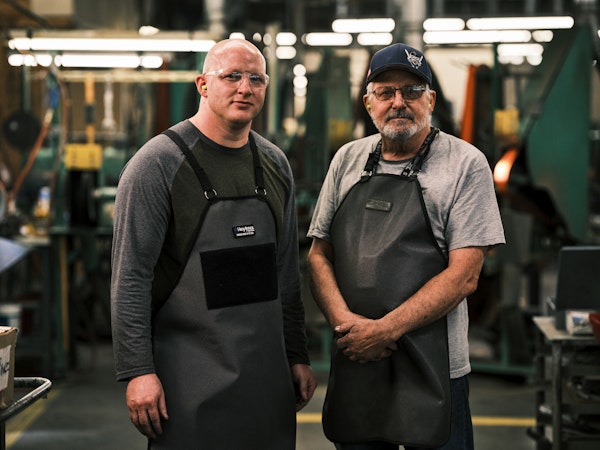
When he started at Buck, Carr wasn’t where he needed to be in life, but the company demonstrated a few principles that stuck with him. He felt like family. Loyalty became a priority and Sam “Lukky” Carr realized something about his own role in knife repairs; “Things can be fixed. Not everything that breaks should be thrown out. People can be changed, people can be restored. You can take something that is broken and make something of it,” Carr asserts. And that is why the Buck Knives Forever Warranty department is unrivaled: the people.